LARGE FORMAT CNC
This week we were introduced to the CNC machine, we created our own designs and cut them using the machine.
What is CNC?
CNC stands for Computerized Numerical Control. It is a computerized manufacturing process in which pre-programmed software and code controls the movement of production equipment. CNC machining controls a range of complex machinery, such as grinders, lathes, and turning mills, all of which are used to cut, shape, and create different parts and prototypes.
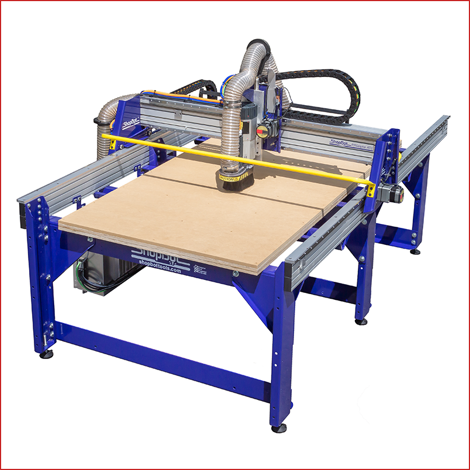
How does it work?
First we started by creating our designs, CNC is a 2d cutting machine so the exported format would be DXF. Personally I like visualizing objects in 3d so I designed my piece as a 3d model and I used Sketchup for that. I don't really recommend using Sketchup, because we faced problems with the DXF file. In our pieces we were asked to use joints to connect the pieces together, the diagram dowwn below helped a lot in the making of the joints and the right size to use.
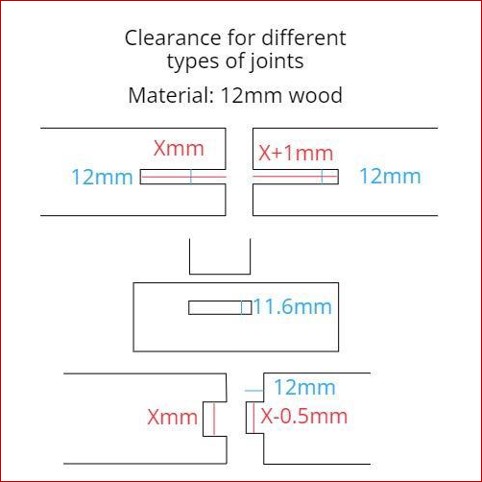
Down below is a picture on the 3d I created in SKETCHUP, the project was a cat tower :) . I used three types of joints, the pocket joint, the normal slide-in joint and lastly the rope joint. I used the rope joints to connect pieces together to make the boxes, scroll down to see how!
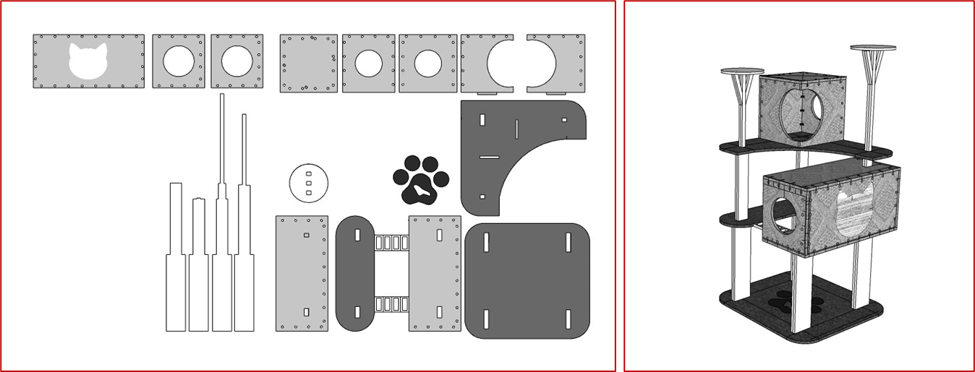
Safety
Down below is a table comparing the different types filaments used in the 3d printers, each filament has its own properties and according to them, we can load the right filament for each product.
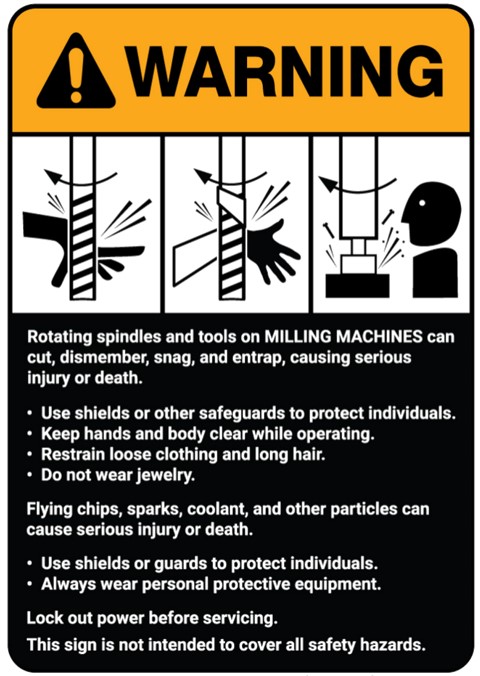
Scroll down to see more.
Group assignment:
In the group assignemnt we tested alignment, speeds, feeds, and toolpaths for the CNC machine. You can find it in Sara's page click here .