Week 3 - Laser Cutting Group Assignment¶
Terminology¶
A laser cutter is a machine that utilizes a focused laser beam to cut, melt, or vaporize materials. These cuts can be used to create precise shapes and designs on flat sheets of various materials. This is done using a laser beam generated which can be of different types, such as CO2 or fiber, depending on the machine and the materials it can cut effectively.
The beam is directed and focused using mirrors or lenses as a sharp focus ensures a clean cut. A computer program controls the movement of the laser head following a digital design that is usually in DXF or DWG format. As the laser beam hits the material, it melts, vaporizes, or burns it away, leaving a clean edge along the intended cutting path. In some cases, an assist gas like oxygen or nitrogen is used to further refine the cutting process.
The result is a precisely cut shape or design on the material sheet. Laser cutters are ideal for creating intricate details and complex patterns that would be difficult or impossible to achieve with traditional cutting methods. They are used in industrial manufacturing, prototyping, jewelry making, sign making, arts and crafts, and so much more.

A laser cutter is characterized by aspects that are crucial for achieving clean and precise cuts.
Focus¶
The focus of the laser refers to how tightly concentrated the laser beam is. Proper focus ensures a clean cut with minimal charring or melting. Some machines have automatic focusing, while others require manual adjustment using a special tool.
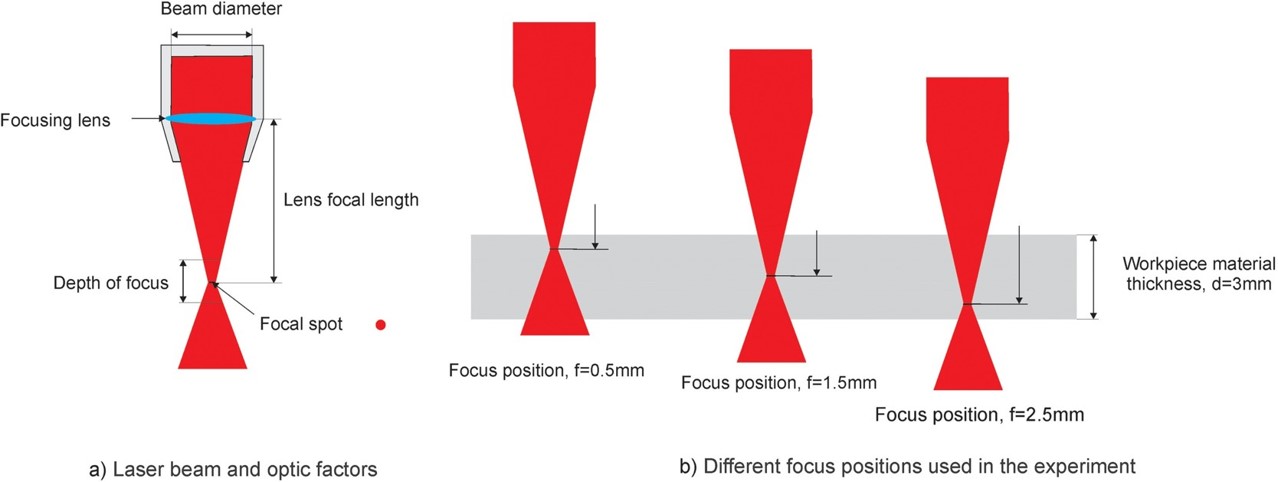
Power¶
The power output, measured in watts (W), determines the intensity of the laser beam and its ability to cut through material. Higher power allows for cutting thicker materials or faster cutting speeds, but using too much power can vaporize or burn the edges. Performing test cuts on scrap material allows a better understanding of the required power to be set for said material.

Speed¶
The speed or cutting rate, expressed in millimeters per second (mm/s) or inches per minute (in/min), defines how quickly the laser beam moves along the cutting path. Higher speeds are desirable but may require more power to achieve a clean cut. Similar to the power, testing cuts with varying speeds on scrap material provides the best data to adjust the machine to the desired requirements.
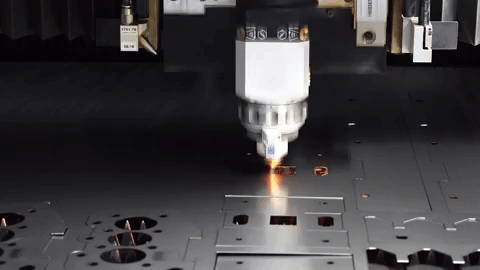
Feed Rate¶
Unlike the speed, the feed rate or the travel rate refers to the overall movement speed of the laser head, including positioning and non-cutting movements. Feed rate is also measured in mm/s or in/min and impacts the overall processing time. Faster feed rates can be beneficial for reducing overall processing time, but it may potentially result in sharp corners and not rounding edges properly.
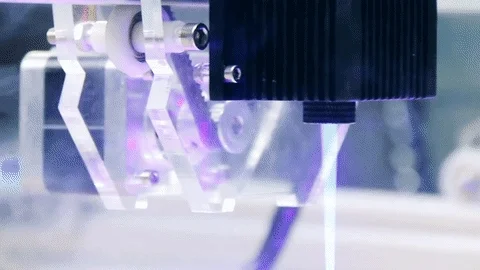
Kerf¶
The kerf is the width of the material removed by the laser cut. It's important to consider kerf when designing parts that need to fit together precisely. Kerf can vary slightly depending on material thickness and laser settings.

Joint Clearance¶
When designing parts for assembly, you need to account for the kerf by adding a small clearance between the parts. This allows for slight variations in kerf and ensures the parts fit together smoothly.
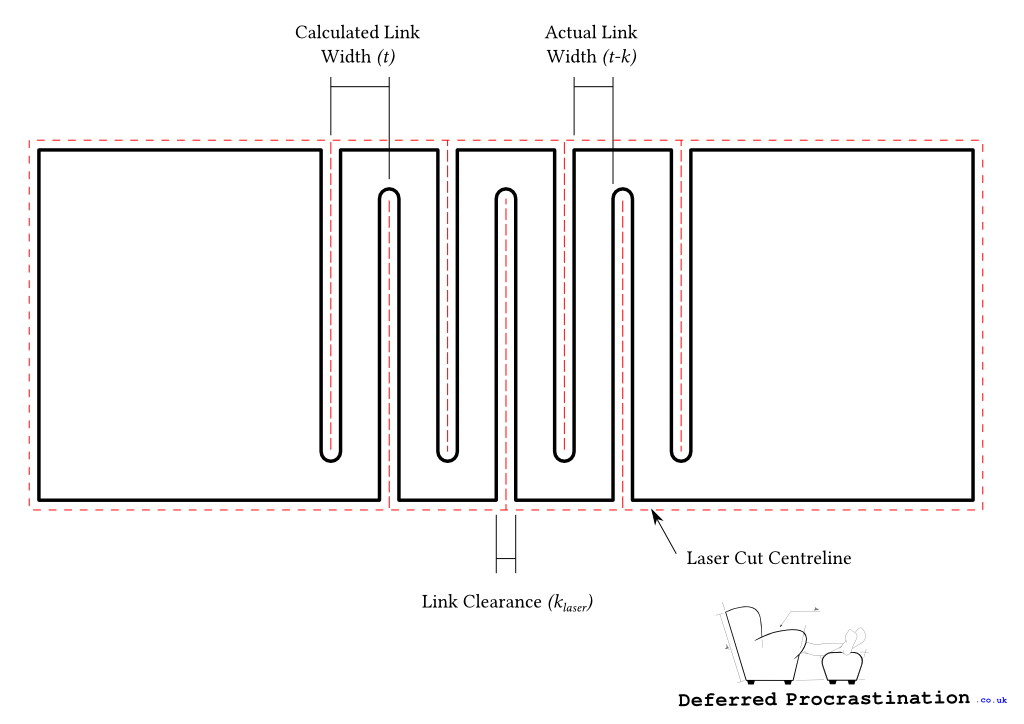
Laser Cutter Types¶
There are several main types of laser cutters categorized by the type of laser they use. Each has its strengths and weaknesses, making them suitable for different materials and applications.
Type | Description | Strengths | Weaknesses |
---|---|---|---|
CO2 Lasers | These are the most established type of laser cutter, using a mixture of carbon dioxide (CO2) gas, helium, and nitrogen to generate the laser beam. |
|
|
Fiber Lasers | A newer technology using fiber optic cables to transmit a high-powered laser beam generated by diodes. |
|
|
YAG (Yttrium Aluminum Garnet) Lasers | These solid-state lasers use a crystal doped with neodymium (Nd) as the gain medium to generate the laser beam. |
|
|

Group Activity¶
The tests that were conducted for our group was on a material made out of cardboard with an approximate thickness of 2mm.
Focal Point Test¶
Adjusting the focal point of the laser achieves a cleaner and more appropriate cut of the material. This is done by adjusting the height (z-axis) of the laser cutting table. The initial test was to understand how the cut will be when subjected to different heights (z-axis). This was performed by setting the scrap material on an incline to determine the most optimal height (z-axis) for the cleanest cut possible.
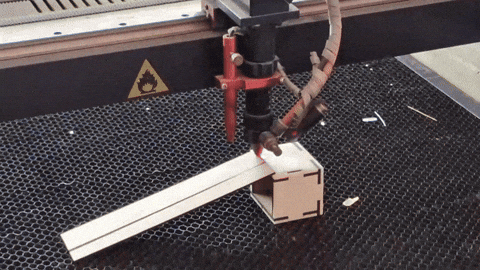

Power & Speed Test¶
The next test performed was to identify the most favorable power and speed the laser cutter should be set at for the specific material. To achieve this, ten different configurations of speed and power have been set on the machine to cut squares. Each square was marked with a specific color on the program (RDWorks V8), then each color was set to have a specific power/speed combination. The optimal power/speed combination determined based on the test was 80/55 since the cut was most accurate and complete relative to the other cuts.
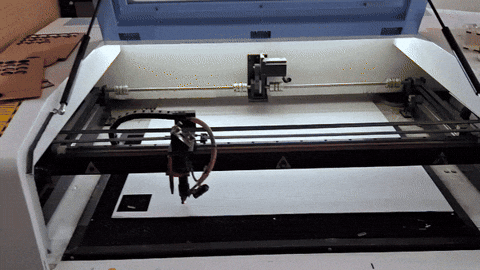


Kerf Test¶
The last test is to check for the joint fitting of the 2mm cardboard. This is to make sure that once the cardboard is joined with another, the clearance is "tight" enough (interference fit) so that the cardboard does not loosely fall out. The way to check this is by making rectangular cut outs of different sizes ranging from 1.4 mm up to 3 mm to check and see which "fit" is best. Based on the test, 1.6 mm is the most suitable cut for this material (2mm cardboard).
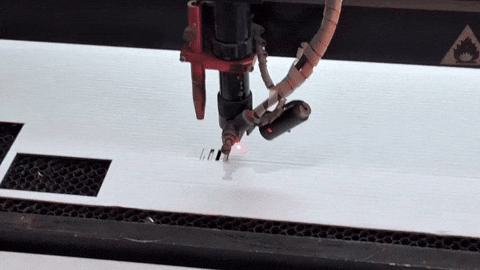


Safety Precautions¶
Using a laser cutter can be dangerous due to the fumes generated from the laser cutting process as well as the chance of the materials catching on fire. Thus, it is important to have safety precautions to reduce any chances of injury:
1-Opening the laser cutting machine ventilation system to extract all of the exhaust gases created from the laser cutting process.

2-Having a fire extinguisher around to be used in the unfortunate case the material catches on fire.
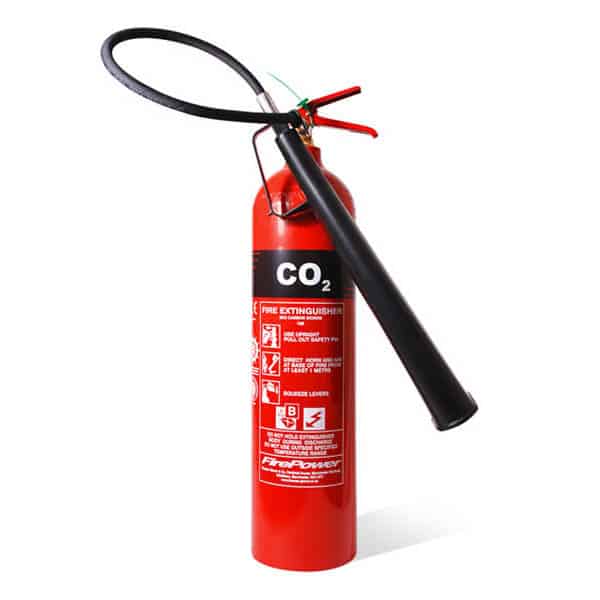
3-Wearing personal protective equipment (PPE) such as safety glasses, safety shoes and lab coats.

4-Using the emergency button on the laser machine to stop it incase anything goes wrong.

Last update:
July 20, 2024